View previous topic :: View next topic |
Author |
Message |
Sanctifier Zorce Moderator

Joined: 07 Apr 2005 Posts: 1794 Location: Good question!
|
Posted: Fri Nov 03, 2006 5:35 pm Post subject: ~From The Archives ~ Roadholding I_Compilation. |
|
|
~From The Archives ~ Roadholding!
Quote: | This is the first in a series of random "tuning" articles that may be of interest to MadMen. |
Okay, we have our ride at last. Now we want to enter Solodex... Want better cornering...
(add your reason here)... Whatever...
This article by an engineer with a Formula 3 background just might give you an "edge."
Roadholding - Denzil Brunning_CCC Mag
Use wisely...
Comments  _________________ Walk softly... and carry a BIG stick! 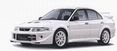
Last edited by Sanctifier on Thu Mar 19, 2009 3:04 pm; edited 5 times in total |
|
Back to top |
|
 |
R. Mutt Jedi Hopeful
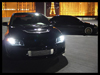
Joined: 14 Apr 2005 Posts: 195 Location: New York
|
Posted: Wed Dec 06, 2006 12:07 am Post subject: |
|
|
"[...] use wider tyres on the heavy end of the car. in this way we would have a beter balance
of tyre area against weight distribution."
Remember Bozz Speed Evo VI RS? lower profile...slightly wider tyres in the front, slightly
'taller'profile in the rear...suspension tuned such that the rear wheels would let go greadually.
I liked that concept. That excerpt reminds me of that approach. Nice post.
Lots of stuff for youngens like me to learn. _________________
 |
|
Back to top |
|
 |
Sanctifier Zorce Moderator

Joined: 07 Apr 2005 Posts: 1794 Location: Good question!
|
Posted: Wed Dec 06, 2006 6:35 am Post subject: |
|
|
^ ^ ^ Yup that's where I first got the idea years ago Mutt.
Reading about the 2000 BozzSpeed Evo 6 reminded me again.
Actually it's the same diameter rims... the RIM WIDTH is 1" narrower in the rear.
This causes a more "rounded" shoulder on the tyre and slightly less tyre contact patch.
It helps the car to rotate easier. So smooth, progressive increase in oversteer.
CCC mag always had some great Tech articles almost every month. Pity they're out of
circulation now. I was trying to scan MGMan's collection but he's sceptical.
Maybe he thinks I'll damage them.
MG all I want is to scan ONE or TWO mags a month... and post the articles on Zorce.
... Then return it and do a couple more... etc. etc. No biggie!
That way silverfish and mold won't destroy valuable information... and 2nrs will benefit too.
Ol' School competition cars... Tuning articles... Tech Advice... all there for everyone to learn.
Maybe some other 2nr can convince him.... Banzai?... Narend?...
MG think about it. I'll scan the DTV SportPart Manual for you to tune the Chevette HSR,
as a reward if you're interested. Remember... only ONE at a time. They'll be safely handled
and returned intact. _________________ Walk softly... and carry a BIG stick! 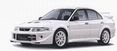 |
|
Back to top |
|
 |
R. Mutt Jedi Hopeful
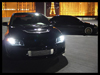
Joined: 14 Apr 2005 Posts: 195 Location: New York
|
Posted: Wed Dec 06, 2006 5:31 pm Post subject: |
|
|
I think that's a great idea...mg man  _________________
 |
|
Back to top |
|
 |
Sanctifier Zorce Moderator

Joined: 07 Apr 2005 Posts: 1794 Location: Good question!
|
Posted: Wed Dec 06, 2006 6:19 pm Post subject: |
|
|
Mutt maybe you could show him that I do this with my mags already on Zorce.
Maybe you could send him a PM. I'm tired trying to convince him.  _________________ Walk softly... and carry a BIG stick! 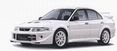 |
|
Back to top |
|
 |
Sanctifier Zorce Moderator

Joined: 07 Apr 2005 Posts: 1794 Location: Good question!
|
Posted: Sun Dec 10, 2006 9:42 am Post subject: |
|
|
Details... Details... DETAILS!
New 2nr wrote: | I know that shocks and springs must be matched properly for best performance.
My question is would the stabiliser bar also need to be matched to the shock and spring? in other
words... would a larger diamater stabiliser bar work with a stock spring and shock
and ... what effects would it have on handling? |
Short answer... Yes it will work, but it isn't optimized.
Long answer.... Sway-bar will increase the effective spring rate of the "inside wheel"
(closer to the apex) when cornering; reducing body-roll.
Therefore it will tend to encourage that end to lose adhesion FIRST.
SET-UP: One school of thought (Colin Chapman - F1 Team Lotus) suggests:
... Stiffer shocks + Softer springs + Adjustable sway-bar. (Stiffness relative to each other.)
Quote: | DETAILS: Stiffer adjustable shocks optimized (compression and rebound) for measured
corner-weight of "race-ready" chassis (including driver's weight in seat)
+ Upgraded spring rate tailored to damper settings
+ adjustable sway-bar. |
This is a Chart (incomplete) that I'm compiling. It might help for basic handling and set-up issues...
 _________________ Walk softly... and carry a BIG stick! 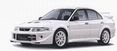
Last edited by Sanctifier on Thu Mar 05, 2009 7:00 pm; edited 5 times in total |
|
Back to top |
|
 |
NarendZORCE Zorce Editor-in-Chief

Joined: 04 Apr 2005 Posts: 3137 Location: In Zorce, usually after the contents page
|
Posted: Sun Dec 10, 2006 10:43 am Post subject: |
|
|
Maybe we could make a Zorce lime and have everyone "bring out the ham."
We could all sit and exchange material and decide what to scan and post. _________________ Drags, Circuit, Solodex, Rally, Karting, the Shows, the Girls, the Car you drive...
ZORCERs done know... the speed lifestyle magazine in the Islands, ZORCE
Click to hear it >> http://www.zorce.com/fortheforums/Zorce15NEW.mp3
Download & SEE iT! >> http://www.zorce.com/fortheforums/Zorce-15.mp4
...........................................................
Oh Yeah! Feel the Rush, it's like... WOW!
May the (Mass x Acceleration)-F+Z be with you... |
|
Back to top |
|
 |
Sanctifier Zorce Moderator

Joined: 07 Apr 2005 Posts: 1794 Location: Good question!
|
Posted: Mon Dec 11, 2006 6:58 am Post subject: |
|
|
I'm game.
EDIT: Sanctifier wrote: | This is the first in a series of "cross-posts" to keep ALL Suspension Tuning & Alignment Data in one thread. |
Link--> Mitsubishi alignment settings, and what they really mean!
Sanctifier wrote: | Q: What are the geometry settings of my car?
A: The geometry settings can make a great difference to the handling on Evo�s so it is
important that they are set up correctly. It is worth getting them checked fairly regularly
(at least once a year although Pirelli recommend every 6 months) and obviously when
you have changed any suspension components. Below are the standard factory settings
but note that the factory set the geometry to a tolerance (not shown below).
A wheel alignment specialist will set it more accurately to a specific figure so even a brand
new car off the production line can benefit with a professional wheel alignment set-up.
For an explanation for the terms used in the table below and for details on how to fine tune
the handling characteristics of your car then see
�Can I improve the handling by changing the wheel alignment?�.... below
Q: Can I improve the handling by changing the wheel alignment?
A: Altering the wheel alignment to improve the handling is probably the simplest, most
dramatic improvement you can make to any car for the cost involved.
First though what is wheel alignment and what do all those terms mean?
Toe
Toe describes the angle at which a wheel sits on a horizontal plane relative to the
longitudinal axis of the car. In other words imagine looking vertically down on top of
a wheel mounted on a car, if the front of the wheel is angled inwards more than the
rear of the wheel then it is said to have �toe-in�, if it�s the other way around then the
wheel is said to have �toe-out�. If the wheel is parallel with the longitudinal axis of the car
then it has zero toe. Toe can be measured in degrees but more commonly, it�s
measured as the distance difference between the front of the wheel rim and the rear of
the wheel rim. Total Toe is the overall distance for a pair of wheels whereas
Individual Toe is half the Total Toe and relates to individual wheels.
Toe-in increases lateral stability but can lead to wear on the inside shoulder of the
tyre. Front end toe-in dampens turn in response but improves the self centring action of
the steering while rear toe-in helps to reduce oversteer due to the improvement in
lateral stability.
Toe-out reduces lateral stability and can lead to wear on the outside shoulder of the tyre.
Front end toe-out can improve turn-in response while rear end toe-out encourages
oversteer due to the reduction in lateral stability.
Toe can be altered on the front by adjusting the track-rod ends and on the rear by
adjusting the toe control arms.
Camber Angle
Camber describes the angle at which a wheel sits in a vertical plane.
Imagine looking at the wheels as you stand in front of the car. If the top of the wheel is
angled inwards, towards the car then the wheel has negative camber, similarily if the
top of the wheel is angled out, away from the car then the wheel has positive camber.
If the wheel sits vertically then it has zero camber. Camber is measured in degrees.
The ideal contact patch of the tyre onto the road would logically be with the wheel in the
dead vertical position (zero camber) so why are most performance cars set-up with
negative camber?
To understand why negative camber is good for performance you have to imagine how
a car behaves during a corner.
With a car set-up with the wheels with zero camber as soon as you enter a corner the
wheel on the outside of the bend (the one that provides the most driving force) will
roll over slightly due to the cornering forces, the body will also roll over.
The tyre on this wheel will no longer have the ideal contact patch on the road, meaning
the cornering performance is reduced. Now if you set the car up with negative camber,
when it enters the corner the wheel and body will still roll over but this time,
if set-up correctly, the wheel will roll over to near zero camber. This means the
tyre contact patch is much better, so cornering performance will improve.
So static* negative camber is used to compensate for body roll, body distortion and
tyre roll when cornering. The downside to all this though is that having the car set-up
with large negative camber means the tyres can wear on the inside edges when driven
in a straight line continually. Setting up the camber is matter of balancing out
the performance gains during cornering with the tyre wear effects on the straights.
*Static means with the vehicle stationary and under no load.
Castor Angle
Castor Angle is the angle to the vertical plane on which the steering axis sits as viewed
from the side. In other words imagine looking at the side of the front wheel,
the Castor Angle is the angle an imaginary line makes that is drawn through the
centre of top ball joint (or top mount of a Macpherson strut) and down through the
lower suspension arm ball joint. Looking on the diagram, if you follow the Castor Angle line
down you can see it hits the ground in front of where the tyres contact with the ground,
this is Positive Castor.
This means the tyres will always follow the steering input or in other words act just
like a normal furniture castor wheel. Castor Angle determines the amount of self-centring
the steering will have, influence the straight-line running and with the Kingpin Angle
it will influence the camber change when cornering as a function of the steering input.
Castor Angle traditionally used to be very small as large amounts of Castor Angle
created heavy steering, now most cars have power steering this is not such a problem.
Large Castor Angles mean greater, dynamic** camber changes can be created and that
means better negative camber when cornering and smaller camber on the straight,
ideal for both performance and wear of the tyres unfortunately too large a castor angle
can lead to poor turn-in.
**Dynamic means with the vehicle moving and under load.
Kingpin Inclination
Kingpin Angle, Kingpin Inclination (KPI) or Swivel-Axis Inclination (SAI)
This is much like Castor Angle, in fact it is exactly the same imaginary line through
the centre of the top ball joint (or top mount of a Macpherson strut) and down through
the centre of the lower ball joint except Kingpin Angle is the angle this line makes to the
vertical as viewed from the front of the car and not the side. The Kingpin angle is set to
try and get the pivot point as close to the tyres contact point on the road as possible (generally).
This is done as otherwise the wheel will �scrub� on ground when turned as the pivot is off centre.
The distance between the point where the Kingpin Angle hits the ground and where the tyre
meets the ground is called the �Kingpin Offset� or �Scrub Radius�. A positive Scrub Radius
or Kingpin Offset is when the Kingpin Angle hits the road surface on the inside of the
centre line of the tyre contact point (see the diagram below), a negative Scrub Radius is
when the Kingpin Angle hits the road on the outside of the centre line of the tyre contact point.
The Kingpin Angle, along with the Castor, dictates the self-centring action of the steering
and the affect the steering will have under braking. Fitting larger wheels can alter the
Scrub Radius if the correct offset is not chosen which in turn can affect the handling.
So what do I set the Geometry too?
Actually there is no one universal answer to this as one person's preference
maybe completely the opposite to someone else's.
For example if someone tells you to run with 2 degrees of negative camber on
the front without asking you how you drive or on what roads then they may just be
condemning your tyres to an early grave if you mainly do motorway miles!
The only advice really is to start with the factory settings, run for a while with those
and then tweak it here and there until you get the right balance for you.
For the Evo�s the only adjustable items are the Front and Rear Toe and Front and
Rear Camber (camber to a lesser degree on the earlier Evo�s). Castor and Kingpin angle
are only adjustable very slightly or not adjustable at all. Castor and
Camber can be adjusted if an aftermarket kit is fitted.
Use the first table as a starting point... then go from there with the detailed information supplied.
For example further 'tweeking' information is available at MLR... Click Here! |
Yeo wrote: | WRT the Evo VII, will the settings be the same for the USDM? |
Sanctifier wrote: | Sorry to take so long to reply. Since E7 is in Table #1, I suppose you meant Evo 8??? |
Sanctifier wrote: | Finally the info requested...
2003 Evolution 8 Alignment Specifications & Procedure - USDM.
Workshop Manual Page #33A-7:
Workshop Manual Page #33A-8:
 |
_________________ Walk softly... and carry a BIG stick! 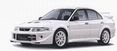
Last edited by Sanctifier on Mon Mar 30, 2009 5:02 am; edited 6 times in total |
|
Back to top |
|
 |
Sanctifier Zorce Moderator

Joined: 07 Apr 2005 Posts: 1794 Location: Good question!
|
Posted: Sun Feb 04, 2007 9:58 am Post subject: |
|
|
Anyway back on topic...
Here's info on the effects of "adjusting" one, two and three-way adjustable dampers...
Quote: | Converting to $TT... ignoring shipping... adding 49.5% (duty + VAT) = $TT.
A 2-way system costs more than $4500+ US = $42kTT +...
A 3-way system can cost more than a good RORO car; $7500+ US = $70kTT +  |
Yup, most 2nrs can't afford two or three-way adjustables but the info will still help with
suspension tuning.
Making It Stick - SCC mag_2-2007 - Page 5.
Hope this helps...  _________________ Walk softly... and carry a BIG stick! 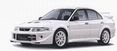 |
|
Back to top |
|
 |
Sanctifier Zorce Moderator

Joined: 07 Apr 2005 Posts: 1794 Location: Good question!
|
Posted: Thu Mar 19, 2009 8:34 am Post subject: |
|
|
Sanctifier wrote: | Another "cross-post" to keep ALL Suspension Tuning & Alignment Data in one thread. |
UPDATE: Okay, so we now have basic info on the following...
Quote: | 1) Suspension definitions... and an idea of the major parts involved...
2) The effect of using different parts on the car's cornering characteristics... (Understeer & Oversteer)
3) The adjustments required for 1- / 2- and 3-way adjustable dampers to refine handling characteristics... |
Now here's info from WORKS on... Choosing the correct spring rate for your vehicle.
Quote: | .......
From answering numerous questions that WORKS customers have posed and the countless conversations
regarding suspension setup, we�ve come to realize that there is much misconception and misinformation
surrounding the topic of spring rates in particular.
The purpose of this paper is to offer a small glimpse of the thought that goes into properly determining the
appropriate baseline spring rates for a track or road-going vehicle.
1. Suspension Frequency and Determining the Wheel Rate.
The first step in choosing spring rates is to choose desired suspension frequencies for the front and the rear.
Suspension frequency is defined as the undamped natural frequency of the body in ride.
Below is the basic equation for suspension frequency, �:
............. where... WR = Wheel Rate
.............................................................. SW = Sprung Weight
For example, the desired suspension frequency for a road going EVO that sees occasional track use can be determined to be approximately 1.6Hz. In contrast, vehicles that are dedicated to track use may have a desired suspension frequency in the range of 2.0-2.5Hz.
Generally, vehicles with aerodynamic aids (higher downforce) will require higher natural frequencies.
Lower frequencies result in a softer suspension with more mechanical grip.
However, the transient suspension response will be slower.
Coming up with the optimal frequencies will depend on the type and efficiency of the vehicle�s aerodynamic aids, among many other factors.
It should be noted that the front and rear frequencies are generally different so that the body�s pitching motion is stalled rather than develop into harmonics. (~ sic Front-to-rear "porpoising motion" on bumpy road.)
The frequency split should be chosen based on the car�s desired use and real world testing and development
-- which take into account the effects of damping (which will not be covered in this paper).
Rearranging the above equation and solving for the wheel rate, WR we have:
.............
2. Finding the Motion Ratio.
The motion ratio is basically the distance the spring moves compared to the distance the wheel moves given the same �bump.� We will choose to find the motion ratio (MR) around static ride height (since the motion ratio is generally not constant over full wheel travel).
To find the motion ratio, the following simple measurements can be made:
Measure the distance from the inner pivot point of the lower control arm to the centerline of the contact patch.
Next, measure the distance from the pivot point of the lower control arm to the point at which the line projected
from the centerline of the spring intersects the line to the center of the contact patch.
Refer to the figure below:
.............
The motion ratio, MR, is simply the ratio of D1 to D2.
Note: Do NOT assume that a MacPherson strut suspension has a 1:1 motion ratio.
A motion ratio of 0.98:1 or 1.02:1 is more typical.
3. Calculating the Spring Rate.
Knowing the wheel rate, WR, and motion ratio, MR, we can calculate the desired spring rate for that particular corner of the vehicle:
.............
However, one must take into account the contribution of the strut to the effective spring rate. Thus, we have to calculate the motion ratio of the strut itself. To calculate the MR of the strut itself, measure the angle of inclination of the strut while the vehicle is at static ride height.
This is not your camber or caster angle, it is the angle of the strut body itself.
The equation for the motion ratio, MR, of the strut is:
.............
This represents the percentage of the force from the spring that is translated into the force that contributes to the spring rate. For example, if by doing this calculation you come up with 98.6%, then that means only 98.6% of the spring force is contributing to the motion of the suspension. So you must add 1.4% to the final calculated spring rate.
Hopefully you have found this suspension information easy to understand and educational. Please stay tuned for more white papers published by WORKS in the future.
Author: Ali Javidan...... Co Author: Eric Shin
Date: 7/14/06................ Copyright WORKS 2006. |
Link--> Choosing the correct spring rate for your vehicle.
Hope this helps... _________________ Walk softly... and carry a BIG stick! 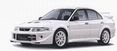
Last edited by Sanctifier on Mon Mar 30, 2009 3:59 am; edited 2 times in total |
|
Back to top |
|
 |
Sanctifier Zorce Moderator

Joined: 07 Apr 2005 Posts: 1794 Location: Good question!
|
Posted: Thu Mar 19, 2009 10:23 am Post subject: |
|
|
Sanctifier wrote: | Yup, another Suspension Tuning "cross-post!"... and for the same reason. |
This WORKS White Paper outlines how to select the correct damper characteristics for your application.
This seems better than the usual "guesstimate" and wasted $$$ that usually happens to most 2nrs...
WORKS wrote: | .......
Choosing baseline damper curves for ride.
Last time, we discussed the process of choosing proper baseline spring rates. In this paper, we will continue the discussion on suspension components by simplifying the process of choosing appropriate baseline damper settings for ride.
What is damping?
In a spring-mass system, any displacement and release of the mass from its equilibrium position will cause the mass to oscillate. If the system were ideal, the mass would continue vibrating at a given frequency (its natural frequency) indefinitely with unchanged amplitude. Introducing damping into the system causes the oscillation to trail off and forces the system to reach a steady state value.
Going back to physics, the simplest equation of a damper is F = CV, where F is the force exerted by the damper, C is the damping coefficient, and V is the velocity of the damper.
So why did we go through all this? In order to introduce the damping ratio � this is where you want to start in determining what kind of damper to use.
Damping ratio.
The damping ratio, usually designated as ζ, is defined as the ratio of actual damping coefficient to the critical damping coefficient. The reason why we work with damping ratios instead of actual damping coefficients is so that we can normalize the discussion for all dampers.
Choosing a damping ratio is a generally a tradeoff between response time and overshoot (you want to minimize both). Typically, passenger cars will use a damping ratio of around 0.25 to maximize ride comfort. For a racecar, the damping must be considerably higher for road holding and control of the unsprung mass motion. Data has shown that for racecars, a good baseline for damping ratio is between 0.65 and 0.70.
Transmissibility.
There is one more concept that should be understood before introducing the damping curve � the concept of transmissibility. Transmissibility is defined as the ratio between output and input amplitude. In our application, the input amplitude will be the height of a road irregularity and the output amplitude is the vertical movement of the car body. For a spring-mass-damper system, transmissibility is actually a function of frequency. Whether you realize it or not, most of you actually know this already from driving cars on the street.
We all know that if you hit a speed bump going very slowly, the car moves vertically almost as much as the wheels. But if you were to go over the same bump going quickly, the body of the car doesn�t move nearly as much. Depending on the speed at which you hit the speed bump, the car body�s response changes. The cause of this phenomenon is that the response of the system � the car and its suspension � is a function of the frequency of the input.
Transmissibility also changes with damping. Included below is a plot of the transmissibility of a spring-mass-damper system for various damping ratios:
.........
For maximum grip, we want to minimize the change in forces that the springs are seeing. This is achieved with minimal body movement. Thus, we want the lowest transmissibility possible. At low frequencies, you can see from the plot that we want higher damping ratios. However, the tradeoff occurs after the crossover frequency, throughout which we would like a lower damping ratio. Corresponding low frequencies to low shock speeds, and high frequencies to high shock speeds, you can see that we need high damping ratios for low speeds and low damping
ratios for high speeds. This concept will be used in determining baseline damper curves.
Determining Baseline Ride Damper Curves;
STEP 1: Calculate the slope of the initial damper curve. This slope applies to both compression and rebound damping.
.........
Side note: This formula for the damping slope comes from the damping term in a simple damped harmonic oscillation.
Here is what the damper curve looks like at this point:
.........
STEP 2: Now we will make some modifications to our initial damper curve.
In compression, energy is �taken up� by the spring, effectively decreasing the damping requirement of the shock in that direction. However in rebound, the potential energy stored in the spring to compress it is released, thus requiring higher damping of the shock in that direction.
This is the reason that shocks typically have a steeper slope in rebound than in compression. Quantitatively, wheel velocities in the compression direction have been measured to be higher than the rebound direction by a factor of about two. Thus, we will modify the slopes by making the rebound slope twice as steep as the compression slope. However, we also want to modify it such that the average slope matches the initial slope that we originally calculated:
......... Compression Slope = (2/3)*Initial Slope.
......... Rebound Slope = (4/3)*Initial Slope
Here is what the damper curve should look like now:
.........
STEP 3: If you remember our discussion on transmissibility, you will note that our damper curve is still not complete � the damping needs to be lowered for high shock speed to minimize the transmissibility there. A good rule of thumb is to reduce the slope by half. The split point between low and high shock speed can be determined based on testing and experience. (Hint: you can also correlate the crossover point on the transmissibility plot to a damper velocity to determine a split point to start from.)
......... Low Speed Compression Slope = (2/3)*Initial Slope.
......... High Speed Compression Slope = (1/3)*Initial Slope.
......... Low Speed Rebound Slope = (4/3)*Initial Slope.
......... High Speed Rebound Slope = (2/3)*Initial Slope.
Here is what the baseline ride damper curve looks like finally:
.........
Side note: The damping curve shown above displays an abrupt transition from high to low damping which for some racing applications may not be optimum, as such a sudden transition can upset the dynamics of the car. One advantage with some �hlins shocks is that they utilize a PCV (parallel compression valve) system that allows a smoother damping transition around the split point as shown by the figure below:
.........
Hopefully you have found this damper information easy to understand and educational. Please stay tuned for more white papers published by WORKS in the future.
Author: Eric Shin............ Date: 8/2/06.............. Copyright WORKS 2006.
References: Brisson, Samuel & Giaraffa, Matt. �Tech Tip: Spring & Dampers, Episode Four� - OptimumG, Denver, CO.
Milliken, Douglas L. & Milliken, William F. "Race Car Vehicle Dynamics." - Society of Automotive Engineers, Warrendale, PA, 1995. |
Link--> Choosing baseline damper curves for ride.
I'll have to read this a few times to be able to apply the info... but it's all good.  _________________ Walk softly... and carry a BIG stick! 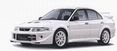 |
|
Back to top |
|
 |
|
|
|
You cannot post new topics in this forum You cannot reply to topics in this forum You cannot edit your posts in this forum You cannot delete your posts in this forum You cannot vote in polls in this forum
|
Powered by phpBB © 2001, 2005 phpBB Group
|